In today’s society, with the rapid development of technology, industries are exploring how to improve work efficiency and accuracy through technological means. A common challenge faced by hotels, hospitals, the military, fire departments, factories, and professional laundry companies is how to effectively manage thousands of work clothes and linens.
These management tasks include handover, washing, ironing, sorting, and storage. Especially in tracking the washing process of each piece of linen, the number of washes, inventory status, and effective classification, there are huge challenges.
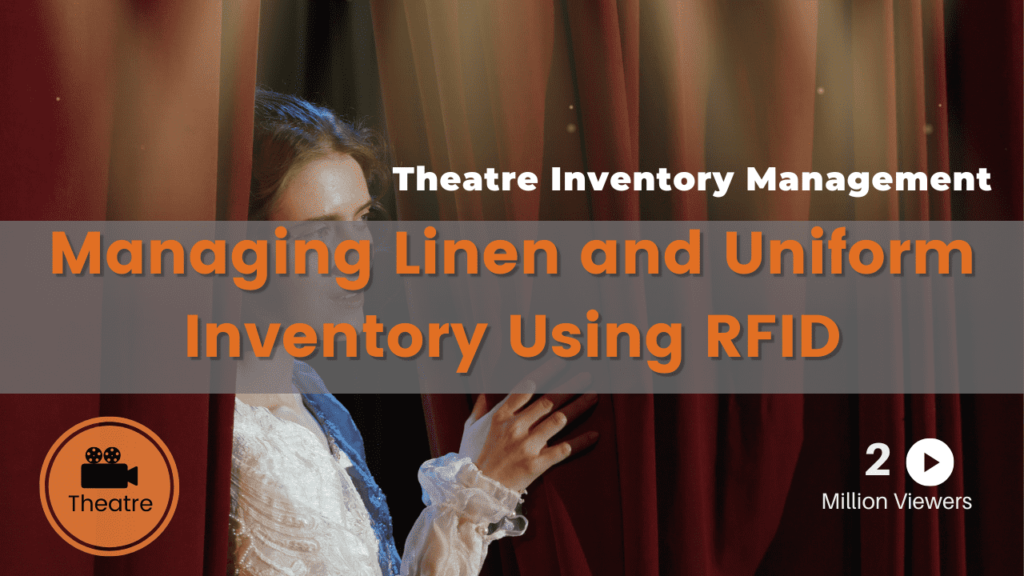
Traditional laundry management methods have several problems:
- The manual registration of laundry tasks is complex, difficult to query, and inefficient.
- Due to concerns about cross-infection, some unwashed linen cannot be counted, which can easily lead to disputes about mismatched numbers.
- It’s impossible to accurately monitor each link in the washing process, and linens may be missed.
- Clean linens cannot be accurately classified, and the minimum safety stock of each piece of linen cannot be accurately arranged.
To solve the above problems, the introduction of professional laundry tags has become an innovative solution. This tag uses ultra-high frequency flexible non-woven wash tags, which are bend-resistant and can be repeatedly rubbed, with a cycle wash count of up to 200 times. They can withstand high-temperature ironing of 120 degrees and can be sewn or hot-pressed into the linen without affecting the comfort of the linen.They can not only withstand various physical and chemical influences during the washing process, but also effectively manage the washing process of the linen without affecting the use and comfort of the linen.
The application of RFID laundry tags has brought linen laundry management into a new era. In the collection, disinfection, industrial washing, sorting, and distribution of clothes and textiles such as hotels, hospitals, and work uniforms, RFID ultra-high frequency laundry tags can quickly complete the inventory and warehouse entry and exit work of laundry items.
In addition, RFID laundry tags can also be used for personnel management in special areas. In situations where it is not suitable to wear a work badge, workers can wear work clothes with embedded RFID laundry tags, and through the association of RFID tags and personnel information, automatic authorization to enter special areas and the calculation of personnel entry and exit time can be achieved.
The use of RFID laundry tags not only greatly improves the work efficiency of laundry management but also greatly reduces the error rate. Through intelligent management, the washing process, the number of washes, and the inventory status of each piece of linen can be accurately tracked, effectively avoiding many problems existing in traditional management methods. In addition, the application of this technology also helps to save labor costs, reduce item loss and damage, and improve customer satisfaction.
In summary, the introduction of RFID laundry tag technology provides an efficient and accurate linen management solution for hotels, hospitals, the military, fire departments, factories, and professional laundry companies. With the continuous advancement of technology and the continuous expansion of applications, the future of laundry management will be more intelligent and automated, bringing more convenience and benefits to all industries.

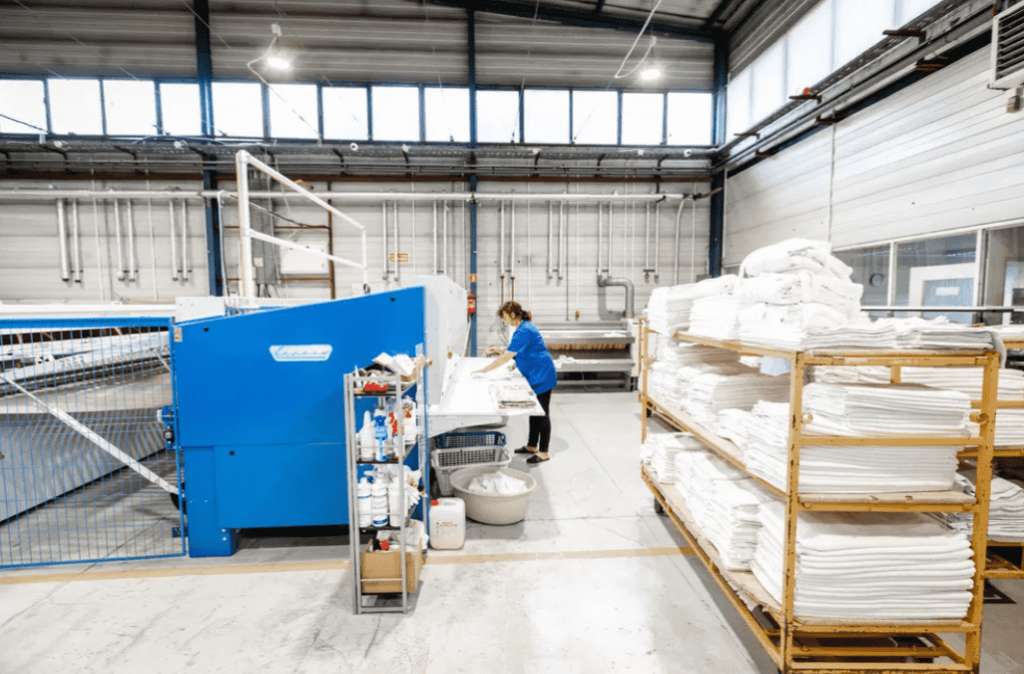

Theatre RFID Inventory Management
Incorporating RFID (Radio-Frequency Identification) technology into your theatre’s inventory management system can significantly streamline the process of tracking props, costumes, sets, and more. RFID offers numerous advantages over traditional barcode scanning, including the ability to scan multiple items simultaneously without direct line-of-sight, enhancing efficiency, especially during check-in and check-out processes. Here’s how you can implement an RFID system in your theatre:
Assess Your Needs
Inventory Size: Determine the volume of items you need to tag. This will help in estimating the number and type of RFID tags needed.
Types of Items: Consider the variety of items (props, costumes, sets) and their material composition, as this influences the choice of RFID tags.
Budget: Factor in the costs for RFID tags, readers, and any software or hardware upgrades required.
- Choose the Right RFID Tags
- Passive vs. Active Tags: Passive tags are cheaper and smaller but have a shorter reading range, while active tags are more expensive, larger, and have a longer reading range.
- Tag Frequency: UHF (Ultra High Frequency) tags are commonly used for inventory management due to their longer read range and faster data transfer rates.
- Form Factor: Tags come in various forms (stickers, hard tags, sew-in labels) suitable for different types of items.
- Select RFID Readers
- Handheld vs. Fixed Readers: Handheld readers offer flexibility and are ideal for manual scans, while fixed readers can automate the process, such as scanning items in/out of a storage room.
- Compatibility: Ensure the readers are compatible with the chosen tags and can integrate with your inventory management software.
- Integrate with Inventory Management Software
- RFID-Enabled Software: Choose software that supports RFID technology. It should allow you to associate each RFID tag with an item in your database, tracking movements, history, and other details.
- Customization: The software should let you customize data fields (e.g., show history, condition, value) and generate reports as needed.
- Mobile Access: For convenience, opt for software that offers a mobile app or mobile-friendly interface for on-the-go management.
- Implement and Train
- Tagging: Systematically tag all items in your inventory with RFID tags. This might be time-consuming initially but is a one-time effort that pays off in the long run.
- Training: Train your staff and volunteers on how to use the RFID readers and inventory management software. Ensure they understand the process for checking items in and out.
- Continuous Improvement
- Feedback: Gather feedback from users to identify any issues or areas for improvement.
- Updates: Regularly update your software and re-evaluate your hardware to ensure your system remains efficient and meets your evolving needs.
Benefits of Using RFID in Theatre Inventory Management
- Efficiency: Quickly scan multiple items at once, reducing time spent on inventory management.
- Accuracy: Minimize human error in tracking items.
- Visibility: Gain real-time insights into where items are, how often they’re used, and their current condition.
- Security: Enhance security by easily identifying missing items.
How Do RFID Asset Tags Work?
RFID asset tags function through a handheld third-party reader that’s connected to your asset tracking application via Bluetooth. The overall functionality remains similar.
Every time an asset’s RFID tag is scanned with the handheld RFID reader, the asset’s last seen location updates, and its profile opens for editing.
Within an asset’s profile, various actions related to your props and costumes can be performed. This includes using the equipment checkout tracking functionality to check out the asset to a user or to someone it has been hired out to.

Implementing RFID technology in the theatre’s inventory management can be a transformative step, making the tracking of props, costumes, and sets more efficient and accurate. While the initial setup requires investment in time and resources, the long-term benefits can significantly outweigh these costs, contributing to smoother productions and better resource management.
To find out more about how RFID can help your applications, please check us catalog.