RFID Tech Boosts Electroplating Efficiency & Safety
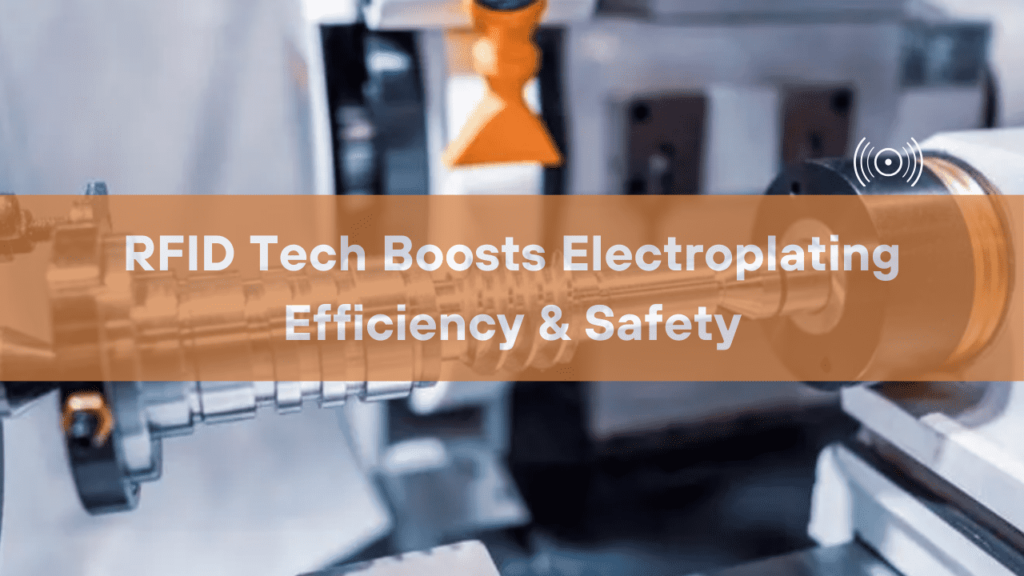
RFID Tech Boosts Electroplating Efficiency & Safety Have you ever considered who uses RFID technology in electroplating production lines and why? This technology boosts automation, enhancing the accuracy and reliability of data collection and streamlining the production process. With RFID tags on products and equipment, users can track and monitor item movements throughout the production process.This technology enables real-time data collection, inventory management, and quality control. These advancements lead to cost savings and increased productivity. Numerous industries, including automotive, aerospace, and electronics, have integrated RFID technology into their electroplating production lines to improve their manufacturing processes. More Information Facebook LinkedIn WhatsApp Radio Frequency Identification (RFID) is an advanced wireless communication technology that can identify specific targets and read related data through electromagnetic fields or radio frequencies, a pr